Silicone glass resin and high temperature resistant silicone mica adhesive.
Huo Changshun and Chen Rufeng from Chenguang Chemical Research Institute, Ministry of chemical industry, etc. are developing silicone glass resin and high temperature mica adhesive in China. In the late 1970s, cts-103 silicone resin, commonly known as "silicone glass resin", was successfully developed by the hydropolycondensation of methyltriethoxysilane in the presence of acid catalyst. The resin was used in the treatment of advanced paper, coating protection of metal surface, and bonding of mica sheet or mica powder in the early stage. In 1980, Sanhua, Xue Zhiqing and Li Yansheng, the resin manufacturers in Shanghai, respectively, used solid cation exchange resin as temporary acid catalyst. The transparent and wear-resistant silicone resins of sar-1 and sar-2 were synthesized by adding a small amount of dimethyldiethoxysilane into the main monomethyltriethoxysilane. There is no residual inorganic acid in the resin, so the storage performance of the product is very stable, and no cementation is found a year later. Due to the introduction of a small amount of difunctional raw materials, sar-2 products are hard, medium and soft, with a wider range of applications. It can be widely used in glass, plastic, metal and other materials, especially for the protection of transparent plastics such as polycarbonate, polystyrene and PVC, and for the moisture-proof and insulation protection coating of electronic components, which will soon form large-scale production.
From 1980 to 1982, Qi hongqiu, Li Yan and Cui Zuoming from Chenguang Chemical Research Institute, and from 1981 to 1983, Xu Zhihong and Xue Zhiqing from Shanghai resin factory used methyltrichlorosilane as the main raw materials to prepare silicone high temperature resistant mica adhesive. The product grades are mr-30 and sar-8 respectively. In addition to the high temperature resistance, electrical insulation, moisture-proof, water-proof and other properties of general organosilicon products, the products also have high adhesion and flame retardant properties. It is mainly used for manufacturing high temperature resistant powder cloud mother board, electronic tube insulation, high temperature resistant powder cloud mother board for support, mica board for turn internal insulation of electric welding machine, etc. Various heat-resistant pigments can also be added as smoke-free and anti-corrosion coatings, and can also be used as incombustible molding composite or ceramic molding resin composed of glass fiber composite laminate and silica. China is rich in mica powder resources, which can be developed into a series of high temperature resistant insulating mica board products.
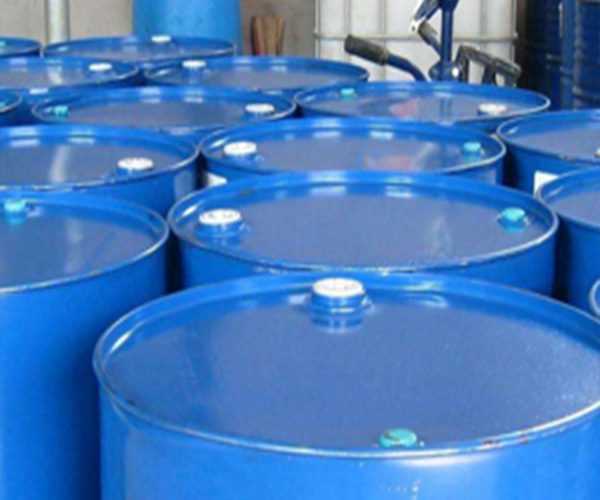
Jiangxi Huahao specializes in the production of dimethyldiethoxysilane
Sar-8 and sar-9 of Shanghai resin factory adopt their own process characteristic route: hydrolyze and alcoholysis organosilicon monomers and concentrate and polycondensate at the same time. Sar-8 and sar-9 were put into production in 1983, and the output has reached nearly one thousand tons. The main raw material of the product is methyltrichlorosilane, so whether mr-30 or sar-8 or sar-9 is produced, the use value of methyltrichlorosilane can be greatly improved.
Organosilicon molding plastics
In 1960s, China's aviation industry urgently needed a kind of arc resistant silicone mold plastic which can withstand strong current and high voltage for making micro switches. Beijing Research Institute of chemical industry has successfully developed silicone resin which is directly hydrolyzed from methyltrichlorosilane and made into arc resistant mold plastic with asbestos filler, which has solved the urgent need of aviation industry. The material was transferred to Shanghai resin factory for production. However, users still need this kind of material, so they have to ask for help from Chenguang Chemical Research Institute, which moved to Sichuan Province. In order to meet the urgent needs of users, Wu Shengquan et al. Of the Institute used the hydrolysis condensation route from methyltriethoxysilane as the starting material to prepare the silicone resin for molding plastics with satisfactory performance, so as to solve the urgent needs of users.
Silicone resin sealing material
In the late 1960s, with the development of China's electronic industry, it is necessary to use silicone sealing materials with excellent electrical insulation, high temperature resistance, moisture-proof and non combustion to package large and small power diodes, triodes, resistors, capacitors, integrated circuits and other electronic devices. In China, Zhang Xinghua, he Jigang, et al. Of the Institute of chemistry of the Chinese Academy of Sciences, and Zhang Jikai, Li Yansheng, et al. Of Shanghai resin factory were early engaged in the development of such resins. They developed a variety of products to fill the domestic gap.
Silicone resin modified coating
The general silicone is mostly composed of polymethylsiloxane and polyphenylsiloxane. The compatibility of silicone resin containing phenyl and organic resin is better than that of methyl silicone resin. The temperature resistance and water resistance of general coatings can be improved by introducing phenyl silicone into them. In the coating industry, high-performance siloxane containing coating can be prepared by blending or copolymerization of phenyl containing silicone resin. As early as the 1960s, Tianjin paint factory and Shanghai resin factory successfully developed the coating of silicone modified synthetic resin. A variety of good properties have been developed, such as silicone modified epoxy resin with good heat resistance and adhesion.
Post time: Sep-24-2022